Back Pressure Valves
The back pressure valve can ensure the stability of the pump system and has an anti-siphon function.
The diaphragm back pressure valve is an accessory valve of the metering pump. The back pressure valve can provide the system with a pressure of 0-3bar to meet the minimum working pressure requirements of the metering pump, ensure flow accuracy, and have an anti-siphon function. The valve is simple, reliable, sensitive, and has excellent corrosion resistance. Robust construction ensures reliability in the rigorous service of municipal and industrial applications.
Metering pump and positive displacement pumps will have excessive delivery when working under low pressure. In order to prevent similar problems, a back pressure of at least 0.7 Bar must be at the inlet and outlet of the metering pump. This can be achieved by installing a back pressure valve in the outlet pipe of the metering pump.
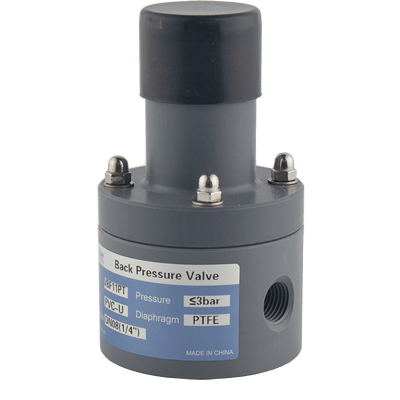
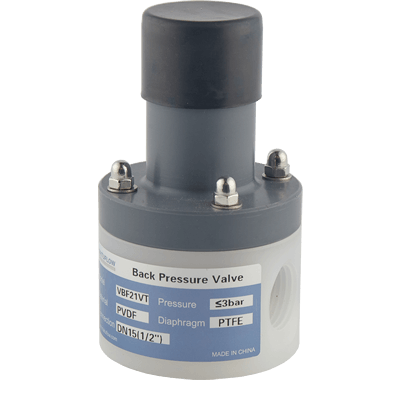
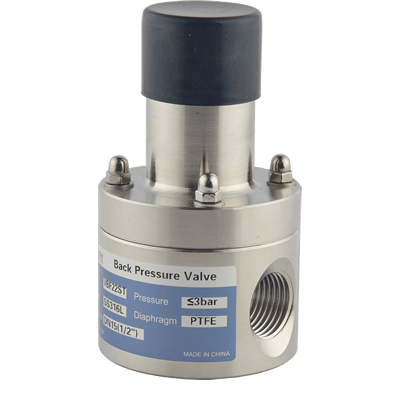

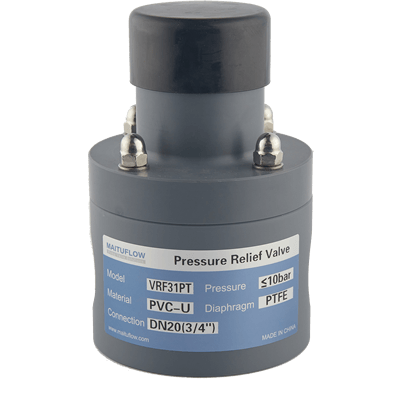
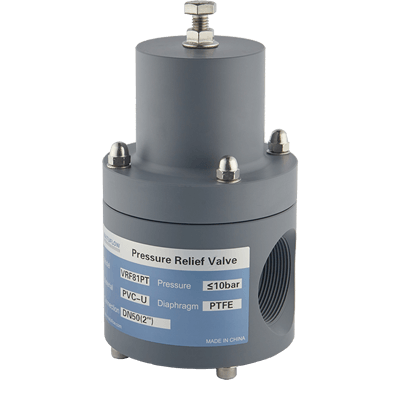
Function
1.Provide pressure difference for the pipes at both ends of the back pressure valve
2. It can be used as a safety valve in systems where the requirements are not very strict.
3.Used in conjunction with a pulsation damper to reduce the harm of water hammer to the system, reduce the peak value of flow rate fluctuations, and protect pipelines, elbows, and joints from pressure fluctuations.
4. Create a good working environment for metering pumps and improve pump performance.
Operational Principle
The back pressure valve works by the elastic force of a spring. When the system pressure is lower than the set pressure, the diaphragm will block the pipeline under the action of the spring force; when the system pressure is greater than the set pressure, the diaphragm compresses the spring, the pipeline is connected, and the liquid passes through the back pressure valve.
Use of back pressure valve
In the outlet pipeline, the back pressure valve should be used at the same time as the pulsation damper, and the pulsation damper should be used to absorb the flow peak between the pump and the back pressure valve. Without the pulsation damper, the back pressure valve will open and close quickly with each pump stroke. When there is a pulsation damper, the back pressure valve will oscillate in the half-open and half-closed positions, so the pulsation damper can reduce the wear rate of the back pressure valve.
For large flow pumps, and the outlet pipe is long and thin, the installation position of the back pressure valve should be close to the filling point to reduce the tendency of siphoning.
When transporting media containing suspended solids, a three-way (or four-way) with a pipe plug should be installed at the inlet end of the back pressure valve so that the pipeline can be cleaned without disassembly.
Back pressure valve is only a kind of pipeline component, and it can only be used in conjunction with other pipeline components (such as pulsation damper, safety valve, check valve, stop valve) in order to exert its maximum effect.
Selection Guide
Adjustable range 0-3bar
Anti-siphon function
PTFE+EPDM diaphragm
Body Material:PVC、PVDF、SS316L
Sizes from ¼” to 2” depending on model
Notice
1. Avoid resonance with the system.
2. When using the pulsating damper, the pulsating damper should be installed between the pump and back pressure valve to absorb the flow peak between the pump and the back pressure valve. Slow down the wear speed of the back pressure valve.
3. should be applied to protective sheds or protective covers when used outdoors.
4. Before any maintenance of the back pressure valve, stop the running equipment, release the pressure, turn off the valve associated with the system, while confirming that there is no pressure in the pulsating damper. Pay attention to preventing the liquid from harming the human body during repair.
5. If the back pressure valve is reversed, the back pressure will be doubled, and the hazards will be hazarded to the system.
6. The failure of the back pressure valve should be cut off in time in operation.
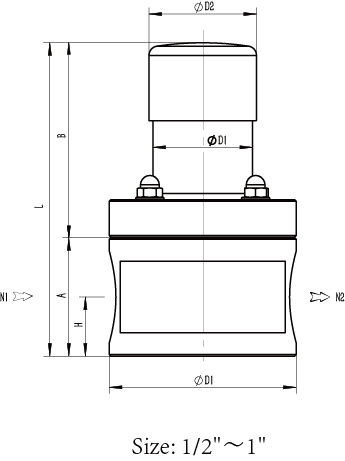
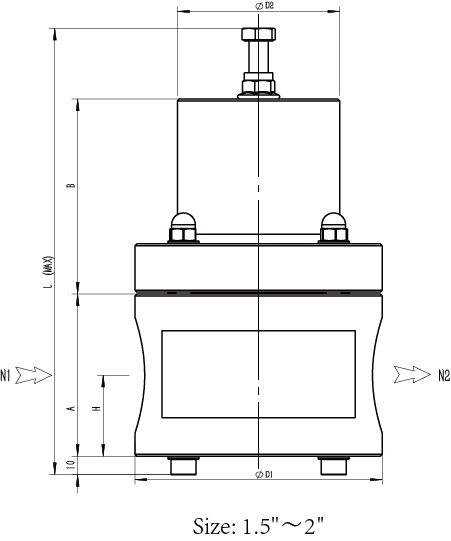
Main Data | |||
Model | Body Material | Size | Max Flow |
VB11PT | PVC | 1/4” | 240L/H |
VB11ST | 316L | 1/4” | 240L/H |
VB11VT | PVDF | 1/4” | 240L/H |
VB21PT | PVC | 1/2” | 380L/H |
VB21ST | 316L | 1/2” | 380L/H |
VB21VT | PVDF | 1/2” | 380L/H |
VB31PT | PVC | 3/4” | 650L/H |
VB31ST | 316L | 3/4” | 650L/H |
VB31VT | PVDF | 3/4” | 650L/H |
VB41PT | PVC | 1” | 800L/H |
VB41ST | 316L | 1” | 800L/H |
VB41VT | PVDF | 1” | 800L/H |
VB51PT | PVC | 1-1/4” | 1200L/H |
VB51ST | 316L | 1-1/4” | 1200L/H |
VB51VT | PVDF | 1-1/4” | 1200L/H |
VB61PT | PVC | 1-1/2” | 2600L/H |
VB61ST | 316L | 1-1/2” | 2600L/H |
VB61VT | PVDF | 1-1/2” | 2600L/H |
VB81PT | PVC | 2” | 3200L/H |
VB81ST | 316L | 2” | 3200L/H |
VB81VT | PVDF | 2” | 3200L/H |
Dimensions(mm) | |||||
L | A | B | H | D1 | D2 |
102 | 38 | 60 | 19 | 60 | 35 |
102 | 38 | 60 | 19 | 60 | 35 |
102 | 38 | 60 | 19 | 60 | 35 |
102 | 38 | 60 | 19 | 60 | 35 |
102 | 38 | 60 | 19 | 60 | 35 |
102 | 38 | 60 | 19 | 60 | 35 |
135 | 60 | 70 | 30 | 88 | 54 |
135 | 60 | 70 | 30 | 88 | 54 |
135 | 60 | 70 | 30 | 88 | 54 |
135 | 60 | 70 | 30 | 88 | 54 |
135 | 60 | 70 | 30 | 88 | 54 |
135 | 60 | 70 | 30 | 88 | 54 |
145 | 70 | 70 | 35 | 100 | 54 |
145 | 70 | 70 | 35 | 88 | 54 |
145 | 70 | 70 | 35 | 100 | 54 |
235 | 84 | 100 | 42 | 128 | 72 |
235 | 78 | 100 | 39 | 128 | 72 |
235 | 84 | 100 | 42 | 128 | 72 |
255 | 95 | 100 | 47.5 | 128 | 72 |
250 | 89 | 100 | 44.5 | 128 | 72 |
255 | 95 | 100 | 47.5 | 128 | 72 |
Body Material | PVC, PVDF, 316L Stainless Steel (SS), additional materials may be available on request | ||||||||
Diaphragm | PTFE+EPDM composite diaphragm | ||||||||
Inlet Type | NPT | ||||||||
Adjustable Range | 0-3 bar | ||||||||
Valve Top | ABS/304SS | ||||||||
Max Temperature | Plastic 45℃, Metal 60℃ |
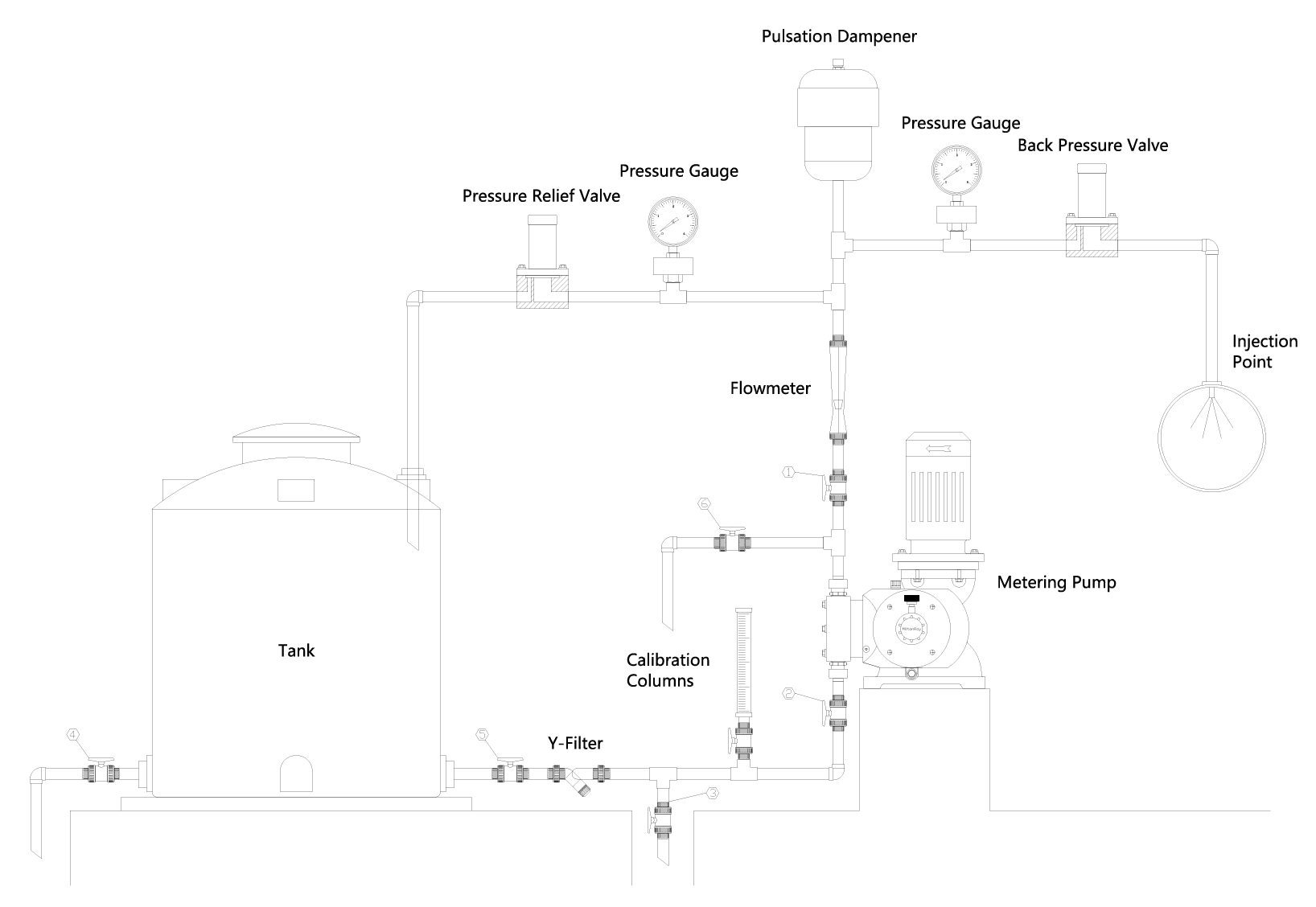